La planta de reciclaje «Junín Punto Limpio», emplazada en una zona rural de este departamento de Mendoza, fue construida en 2012 durante la gestión del ex intendente local Mario Abed. En mayo pasado, gracias a la continuidad del proyecto, hoy a cargo del actual intendente Héctor Ruiz y su equipo, obtuvo el galardón internacional «Premio Verde 2022», a la mejor iniciativa social y ambiental de Iberoamérica, por su plan de reciclaje de luminarias.
Desde su entrada en funcionamiento a la fecha, la planta ha recolectado unos 90.000.000 de envases de plástico y los ha reciclado en distintos objetos útiles, muchos de los cuales vuelven a la comunidad en donaciones y otros se venden mediante mecanismos de tercerización a precios convenientes. En su último programa, Junín Punto Limpio está retirando y procesando antiguas luminarias que contienen sustancias dañinas para el medio ambiente como sodio y mercurio, y reemplazándolas por luminarias nuevas fabricadas allí mismo.
En ocasión de celebrarse el Día Mundial del Medio Ambiente, el 5 de junio, la comuna de Junín invitó a la prensa de Mendoza a una recorrida por su planta de reciclaje Junín Punto Limpio, un orgullo provincial y nacional que acaba de ser reconocida en Miami, EEUU, con el galardón «Premio Verde 2022» como la mejor iniciativa en beneficio del ambiente entre 500 iniciativas y proyectos de toda Iberoamérica. Su creación y funcionamiento se basan en una política de Estado municipal, fundamentada en la gestión integral de residuos sólidos urbanos y su posterior disposición final. Así han recolectado y convertido en objetos útiles para la comunidad unos 90 millones de envases plásticos.
En la actualidad, la planta Junín Punto Verde recicla diariamente 2,5 toneladas de plástico.
Los residuos son trasladados a la planta de reciclaje, donde se acopian y compactan para el procesamiento. Los materiales provenientes de envases PET (jugos, aguas, gaseosas) se trituran y se destinan a la elaboración de ladrillos, y las bolsas o envases de polietileno o polipropileno se utilizan para producir mangueras para conexiones de agua, tejas, maderas plásticas y prótesis, éstas últimas a través del uso de la tecnología de impresión 3D. Con los materiales de construcción ya se han levantado 6 viviendas sustentables.
Según datos del Departamento General de Irrigación, con este programa en Junín se logró reducir hasta un 80% los residuos plásticos en los cauces de riego, posibilitando así la fluidez del agua y evitando el derroche hídrico.
Por otro lado, se montó la primera planta de reciclado de luminarias del país, en instalaciones dotadas con tecnología de avanzada donde se reciclan los tubos de vapor de sodio a tecnología led, dando disposición final a los residuos eléctricos y electrónicos. Al mismo tiempo, las carcasas de plástico antiguas se recomponen para volver a utilizarlas.
Hasta hoy, en la planta Junín Punto Limpio se elaboraron 250.000 ladrillos PET, 3.000 tejas aislantes, 8.000 palos de viña, 1.500 útiles escolares y 3.600 luminarias LED.
En el mes de mayo, la Municipalidad de Junín fue premiada en la 9na. edición del certamen Premios Verde 2022, dentro de la categoría Políticas Públicas, que merituó entre otros factores y beneficios para el ambiente el impacto generado en materia de sostenibilidad con el reciclado de luminarias de sodio en ese departamento. Los Premios Verde surgieron en 2013 en el marco de la Cumbre Internacional de Medio Ambiente y desde entonces permitieron dar visibilidad a los mejores 500 proyectos sociales y ambientales de Iberoamérica.

Durante el recorrido por la planta, Daniel Ascurra -diseñador industrial y jefe de la planta de reciclado-, Héctor Ruiz -intendente de Junín-, Ricardo Morcos -presidente del Concejo Deliberante de ese departamento- y Mario Abed -ex intendente de Junín y actual vicegobernador de Mendoza- explicaron cada uno de los procesos que se llevan a cabo en el establecimiento.
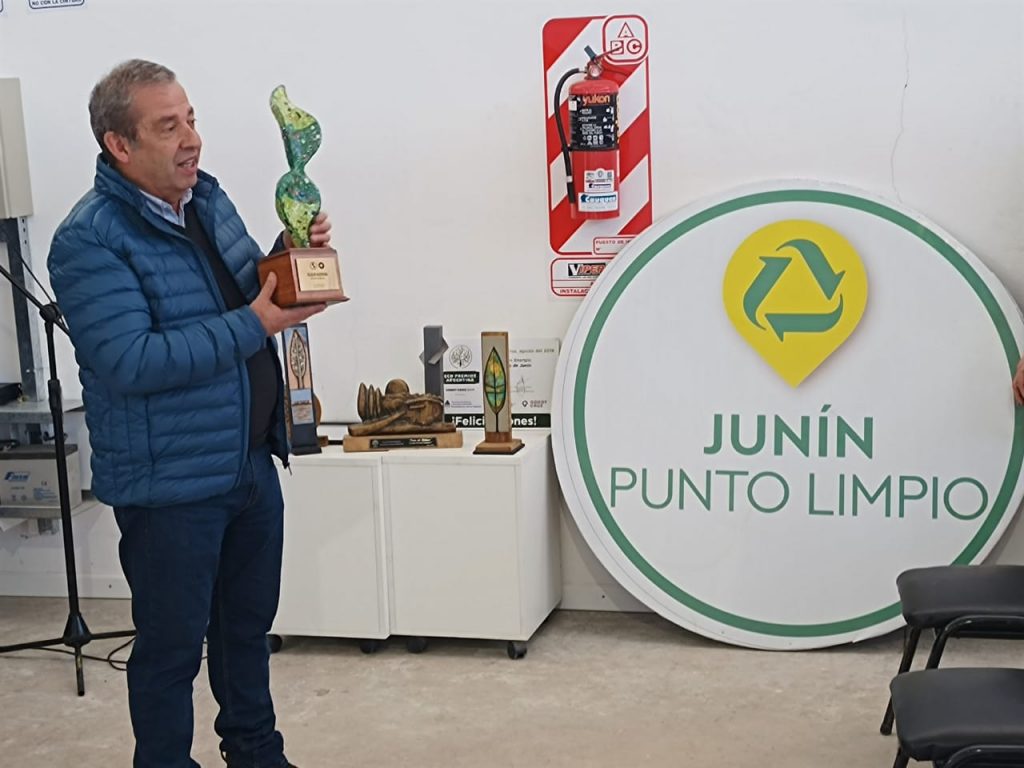
Argentina se encuentra entre los países de América Latina con el mayor consumo de plásticos por habitante, con un valor de 42 kg por año.
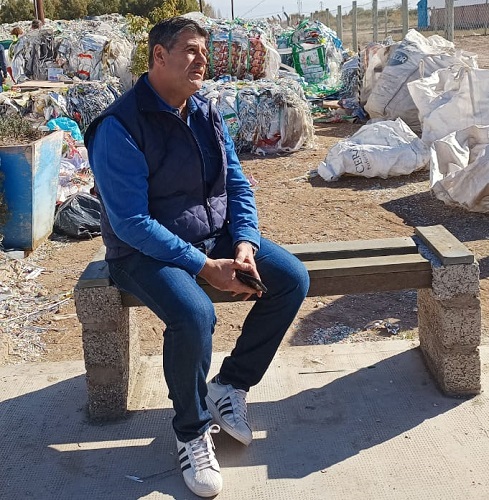
Ladrillos ecológicos
Se fabrican mediante una mezcla de materiales con dosaje calculado para la resistencia técnica de mamposterías en la construcción de viviendas, con una cantidad equivalente a 40 botellas plásticas cada uno, lo que genera el volumen idéntico a los ladrillos convencionales.
El producto cuenta con el patentamiento del Conicet y está aprobado para la construcción de viviendas y edificios por la aptitud física del producto. Hasta la fecha, el municipio lleva construidas 6 viviendas sustentables e innumerable cantidad de ampliaciones y mejoras edilicias en general. Esta forma de producción reduce notablemente el impacto ambiental generado en la producción convencional, ya que evita la quema de madera y, por consiguiente, la tala indiscriminada de árboles; suprime el desgaste del suelo; no expulsa gases a la capa de ozono y reduce la cantidad de agua utilizada en el proceso, siendo nuestro producto tan eficaz como el proceso mismo.

Viviendas sustentables
A partir de un plan de viviendas municipal, ya se entregaron 6 viviendas de 56m², las que constan de 2 dormitorios, baño y cocina/comedor, construidas con:
– 4.000 ladrillos PET conformando la mampostería, elaborados a partir de 160.000 botellas y envases, equivalentes a 4.800 kilos de desechos plásticos recuperados de la vía pública y causes de riego.
– 1.000 tejas plásticas provenientes de 2.000 kilos de polipropileno reciclado
– 2 paneles solares de 350 watts cada uno.
– Iluminación LED que consume entre 2 y 5 veces menos que una lámpara de bajo consumo convencional.
– Estufa de doble combustión junto a briquetas elaboradas con restos de poda del arbolado público, emanando calor entre 6 y 7 veces más que las estufas abiertas, consumiendo menos material combustible, ya que aprovechan la temperatura almacenada sin generar pérdidas y reducen la emisión de dióxido de carbono entre 14 y 20 veces.
– Accesorios de electricidad y cerrajería realizados con 1kg de plástico en impresión 3D.
Tejas, madera plástica y mangueras
Se fabrincan mediante la extrusión del plástico, con salida a moldes predeterminados para el producto requerido. De esta forma, a las viviendas construidas se le suman estos productos e impresión en 3D para cerrajería y conexiones eléctricas, arrojando como resultado final un tipo de vivienda entre los más sustentables de América Latina. Son casas construidas en un 60% con desechos plásticos, adosando en ella elementos de eficiencia y ahorro energético, como paneles solares, precalentadores solares, iluminación led y estufas ecológicas de doble combustión.
Las tejas sustentables Mangueras para riego o agua potable
Para su elaboración, al municipio de Junín se sumaron Electromecánica Bottino y Bonomini del Mercosur SA, las que tuvieron a su cargo la elaboración de un molde que pudo mejorar la cantidad de tejas elaboradas por día. Además, se incluyó la participación de la empresa Baresi SRL, de Maipú, que se encarga de elaborar los pele (pequeñas lentejas de plástico) que son inyectadas en las tejas, dando otra calidad al producto final. El municipio, a cambio, se hizo cargo de los residuos plásticos que generan las empresas.
Se producen 36 tejas por hora, consiguiendo en 24 horas la cantidad necesaria para poder construir un techo de 66 m2.
La producción de maderas plásticas está en manos de la empresa privada Maderas Plásticas Mendoza, que desarrolla productos que reemplazan a la madera, reduciendo así la tala de árboles, tales como:
- Postes plásticos para viñas
- Postes plásticos para campos
- Cierres perimetrales para barrios privados
- Tablas y perfiles
- Mobiliario urbano
La materia prima que ingresa es separada en dos tipos de plásticos: flexibles y duros. Ambos tipos son triturados en un molino a cuchillas. Luego, todo el material molido se mezcla e ingresa al proceso de extrusión. La extrusora tiene una capacidad máxima de procesamiento de 500 kg/h. El siguiente proceso consiste en el enfriamiento del material que ingresa a los moldes; el enfriamiento se realiza con agua que se recircula constantemente. La generación de residuos durante la fabricación de los postes es mínima, debido a que casi todo el material se aprovecha, inclusive los postes defectuosos.
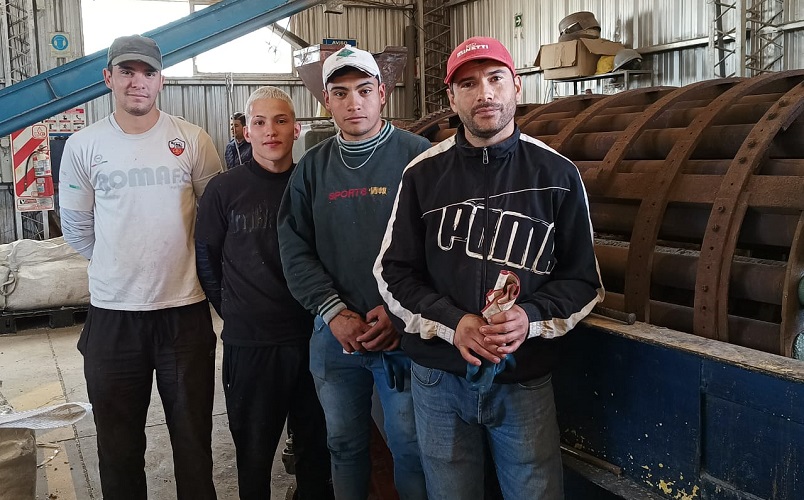
Luminarias reconvertidas
El proceso de reconversión reutiliza y recicla la carcasa original existente, los tornillos, las borneras, cables, chapas, soportes, conectores y demás insumos; el artefacto es desarmado completamente, pasando por un proceso de limpieza y desarme total, luego por arenado y pintura para finalmente unir las piezas de la nueva tecnología LED con los mismos insumos mencionados anteriormente. La separación de los materiales forma parte fundamental en el traslado a la disposición final de elementos, desde la pantalla de aluminio, el acrílico o vidrio protector y los residuos eléctricos recuperables (balastos, porta-focos, etc.); posibilitando el tratamiento de una gama de residuos que aún resultan habituales.
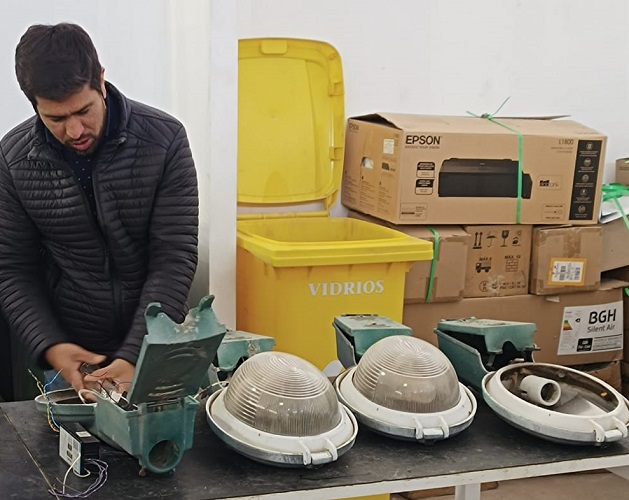
En cuanto a la lámpara de vapor de sodio (constituida en promedio por 93% de vidrio, 5% de metales ferrosos y no ferrosos y 3% de polvos y gases), aquellas que aún tengan su ciclo de vida útil se destinan a la reutilización, a diferencia de un ínfimo porcentaje inutilizable que se procesa en maquinarias específicas, donde se tritura y disminuye el volumen en piezas muy pequeñas y son acumuladas en un cilindro estándar de metal.
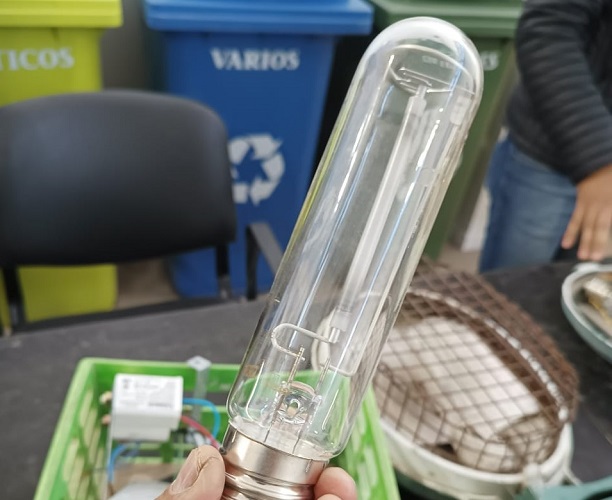
Al mismo tiempo, el vapor y otras partículas contenidas de las lámparas son capturados por un aspirador, que consiste en el subsistema de aspiración constante con método de filtración de alta eficiencia HEPA. En una etapa final, el carbón activado especial captura el vapor encapsulando el mercurio. Esto nos permite separar los materiales que componen las lámparas para reincorporarlos en el ciclo del proceso de fabricación, tanto de vidrios como de metales no ferrosos. Por otro lado, en lo que respecta a porta-focos, son desarmados para continuar con el circuito de separación de materiales, teniendo como destino la reinserción de metales a la fabricación de los mismos, así como la trituración del cerámico con el mismo fin.
Las placas LED que se utilizan en el ensamblaje son impresas en PCB de industria nacional, prescindiendo del driver controlador, y cortadas a medida localizada por plasma, permitiendo ser amoldadas en todo tipo de carcasas a disposición, adecuadas para luminarias en plazas, paseos, avenidas, autopistas, barrios, parques, etcétera.
Las carcasas reacondicionadas Una placa LED que no utiliza driver
La característica principal de la nueva tecnología gira en torno a la eficiencia en el consumo energético: cada lámpara posee dos sistemas integrados que juntas generan una potencia de 86 Watts con una medición de 12.000 lúmenes, a diferencia de las lámparas de vapor de sodio que generan un consumo de 250 Watts. Esto último significa un 60% de ahorro energético, con una durabilidad de aproximadamente 13 años de iluminación, en comparación a los 6 años de durabilidad de una lámpara convencional; produciendo estabilidad en la red de tendido eléctrico que previene el calentamiento de transformadores y roturas de fuentes, servidores y protecciones.
Impresión 3D para objetos útiles
Dentro de la planta existe un área de desarrollos en impresión, que aplica la la tecnología de impresión en 3D para la manufactura de elementos y accesorios útiles en la vida cotidiana, utilizando máquinas especialmente diseñadas que, a través de la impresión aditiva, realizan depósitos repetitivos de capa sobre capa de material plástico. Así, transforman una imagen plana sin relieves a un objeto con altura y profundidad, es decir un cuerpo con tres dimensiones. Para lograr la producción de elementos se utilizan distintos software de diseño gráfico, los que brindan la posibilidad de recrear en pocos minutos las ideas plasmadas en papel en un objeto físico tridimensional.
Impresoras 3D Una prótesis made in Junín Punto Limpio
Este área resultó fundamental para el desarrollo de maquetas y planeamiento de matrices en el proceso de inyección de plástico, facilitando la producción de diversos productos, obteniendo excelentes resultados eficientes a bajo costo y gran escala de producción. Cuenta con tres máquinas de impresión que funcionan con baja temperatura, no emanan gases contaminantes y trabajan con material biodegradable.
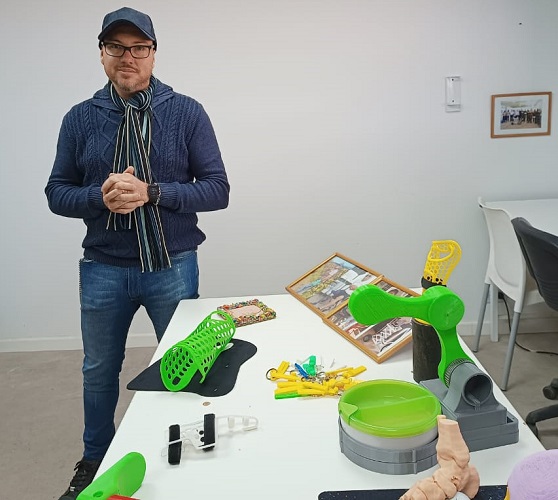
Los productos resultantes son destinados específicamente a la educación ambiental, capacitación de distintos actores sociales, exposiciones, fabricación de juegos didácticos, instrumentos musicales y merchandising empresarial, todos ellos distribuidos en diferentes instituciones educativas y Centros de Día locales, los que luego las comercializan a instituciones privadas, recibiendo el financiamiento correspondiente por el trabajo realizado. Principalmente, esta tarea se lleva a cabo mediante personas con diferentes discapacidades, quienes además de generar una economía propia realizan actividades didácticas importantes para la recreación.
Junín forma parte del programa «Plazas de la Felicidad» de Coca-Cola, instalando juegos elaborados con material PET reciclado.
Del mismo modo, en la Planta se elaboran mobiliarios urbano y escolar, juegos recreativos y elementos viales. De esta manera, reductores de velocidad, cartelería vial, cestos de basura, bancos de plazas, toboganes, calesitas y farolas, entre otros elementos, forman parte del nuevo paisaje urbano de Junín.
Además de las maquinarias descritas anteriormente, funcionan en la planta otras tres, con más capacidad de procesamiento, destinadas a la fabricación de matrices para productos usuales y a la producción biomédica.
En cuanto a este último punto, se realiza en conjunto con profesionales de la salud, porque algunas de las impresiones en 3D se utilizan en procedimientos quirúrgicos como modelos a escala obtenido de tomografías computadas, respetando genuinamente las partes afectadas, lo que facilita al personal médico una mejor vista sin invadir la zona completa, logrando una mayor recuperación y eficiencia en la operación.

Este tipo de impresión también permite elaborar modelos de prótesis, desarrollando prototipos articulados según dimensiones específicas de los pacientes. Se diseñó, por ejemplo, un dispositivo para movilidad asistida eléctricamente que cuenta con un sistema de cuadro tipo triciclo con tracción eléctrica en una de sus ruedas y batería de ion de litio, de fabricación en acero y rodado de bicicleta o similar, el que posibilita movilizarse por diferentes superficies con total autonomía. Se adaptó al chasis un sistema elevador eléctrico, con un segundo motor de 350 watts, relacionado para soportar un peso promedio de 50 kilos.